Are you grappling with inefficiencies and high costs in your manufacturing process? If so, you’re not alone. Many manufacturers face challenges in maintaining consistent product quality and meeting production demands. If these challenges sound familiar, it might be time to consider automated assembly line solutions. Production line automation is revolutionizing the industry. It offers various advantages in precision, speed and scalability.
This guide provides the insights you need to make informed decisions and stay competitive in a rapidly evolving market.
The Basics of Assembly Automation
Assembly automation utilizes technology and machinery to perform tasks with minimal human intervention. Various components are used in assembly automation to streamline processes and increase productivity. They can consistently and accurately help with part handling, welding, fastening and inspection.
For instance, robotic arms can help perform precise tasks like assembly or product inspection. Vision systems can also inspect and guide components. There are other components, such as automated guided vehicles (AGVs) and conveyor systems.
Note that manufacturing automation encompasses the entire production process. On the other hand, assembly automation focuses on making components into final products.
Assembly automation can also be implemented differently, depending on the application’s requirements. The types include:
- Fully-automated systems: Entirely automated with no human intervention
- Semi-automated systems: Combine automated and manual processes
- Fixed automation: Designed for high-volume, repetitive tasks
- Flexible automation: Adaptable to various tasks and product changes
- Lean automation: Focuses on efficiency and waste reduction
Choosing the Right Assembly Automation for Your Manufacturing Process
There are several factors manufacturers must consider holistically. These factors are categorized into assembly processes and other business aspects.
Assembly Process Factors
The assembly process-focused factors can include the following:
- Material and size: It’s crucial to understand the material’s thickness, part length and width. Different materials and sizes may need specific types of automation equipment.
- Part volume: The volume of parts to be produced affects the automation choice. High-volume production may justify the investment in advanced automation systems. Lower volumes might require more flexible, cost-effective solutions.
- Part complexity: The complexity of the parts influences the type of automation needed. Complex parts require sophisticated machinery to handle intricate tasks, while simpler parts only need basic automation.
- Welding automation: This is for processes involving welding. The type of welding and the material properties must also be considered when selecting the suitable automation technology.
- Fastening automation: If the assembly involves fastening components, the choice depends on the fastener type and the required precision and speed.
Decision-Making Factors
Other factors may impact one’s decision, such as:
- Cost and ROI: Evaluate the initial investment and ongoing operational costs against the expected return on investment (ROI). This includes considering direct costs — like equipment and installation — and indirect costs — like maintenance and training.
- Design variability: Manufacturers must also consider the automation system’s flexibility to handle design changes or multiple product variations. Systems that can adapt to different designs offer enhanced long-term value.
- Quality: It’s essential to ensure that the chosen automation technology can maintain or improve product quality. This includes precision, consistency and the ability to detect and correct defects.
- Scalability: The ability to scale the automation system up or down based on production demands is important. Manufacturers must be able to accommodate according to future growth or changes in market demand.
The Advantages of Assembly Line Automation in Manufacturing
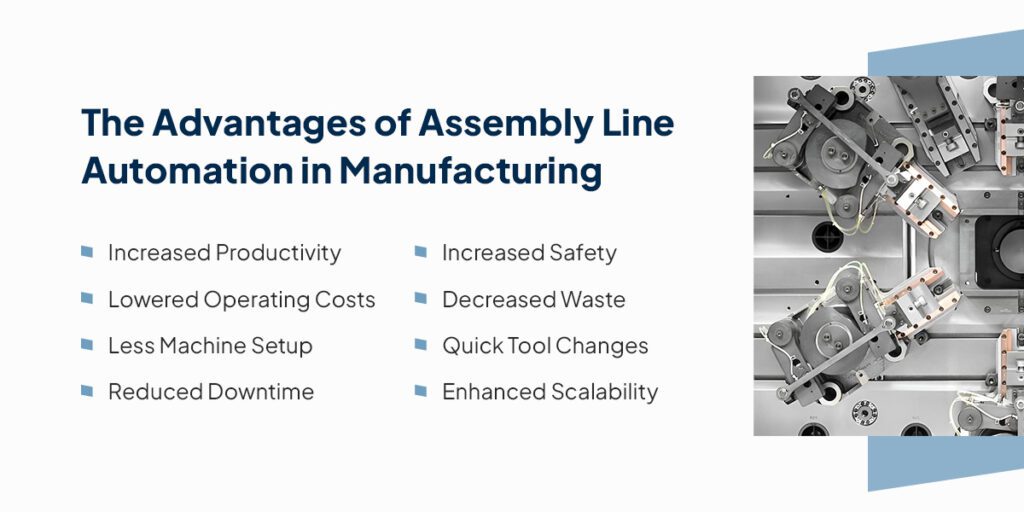
Assembly line automation offers numerous advantages that, when utilized, can create a more holistic and effective manufacturing environment.
Increased Productivity
Machines can work 24/7. They can operate continuously without fatigue — no need for ending shifts, meal breaks or vacation days. Manufacturers using automated machines can thus operate longer and produce more than they could with manual practices alone.
Lowered Operating Costs
Assembly automation can lower operating costs over time. While the up-front investment can be high, it eventually pays for itself. For example, automation reduces the need for manual labor, leading to cost savings on wages and benefits.
Less Machine Setup
Automated systems can quickly switch between tasks and product configurations with minimal setup time. This flexibility allows manufacturers to respond more rapidly to changing market demands.
Reduced Downtime
Predictive maintenance technologies integrated into automated systems can help anticipate equipment failures before they occur. This proactive approach minimizes downtime and ensures production schedules remain met.
Increased Safety
With increased automation involvement, there is a reduced need for human intervention in hazardous tasks. Automated systems can handle dangerous materials and perform tasks in environments unsafe for human workers. It could lower the risk of workplace accidents or injuries.
Decreased Waste
Integrating assembly automation can help enhance material and time usage while ensuring the highest production level. Optimizing resources can allow manufacturers to minimize their environmental impact and improve sustainability.
Quick Tool Changes
Automated systems can incorporate quick-change tooling solutions. This advantage allows for rapid adjustments and minimal production bottlenecks. Quick tool changes are crucial for short production runs and frequent product variations.
Enhanced Scalability
Automated assembly lines can be scaled up or down to match production demands. Manufacturers can add or remove machines and adjust processes to accommodate different production volumes without significant downtime or reconfiguration.
Integrating Assembly Automation into Existing Manufacturing Processes
Here are a few key steps to follow when integrating production line automation:
1. Planning and Assessment
Begin by conducting a thorough assessment of the current manufacturing processes. Doing so will help to identify areas that can benefit from assembly automation. Manufacturers must also evaluate the feasibility of automation for specific tasks and consider factors such as part complexity, production volume and material requirements.
Next, develop a detailed plan that outlines the facility’s automation goals, budget, timeline and the expected ROI. Engaging with stakeholders and gathering input from various departments can help create a comprehensive and realistic plan.
2. Design and Integration
The next step is designing the automation system tailored to the facility’s needs. This involves selecting appropriate automation technologies, such as robotics, conveyor and machine vision systems. They’ll also need to collaborate with automation experts to ensure the design aligns with production requirements and integrates with existing equipment.
Once the design is finalized, the integration process will begin. This phase may involve installing new machinery, updating software and configuring systems.
3. Training and Implementation
Train the workforce to operate and maintain the new automated systems. Focus on emphasizing safety protocols and troubleshooting procedures in these trainings. Manufacturers can implement the automation system in phases, starting with a pilot run to identify and address any issues. Gradually scale up the automation while monitoring performance and making necessary adjustments to optimize efficiency and productivity.
4. Maintenance and Support
Establish a robust maintenance and support plan to ensure long-term success. Regularly scheduled maintenance and quick repairs are essential. Together, they can help minimize downtime and extend the life span of equipment. Manufacturers can create a support team or partner with service providers to handle technical issues.
5. Safety
Safety remains a priority. Conduct a comprehensive risk assessment to identify potential hazards and implement mitigation measures. This could include installing safety guards, emergency stop buttons and implementing proper signage. Additionally, training employees on safety protocols and reviewing safety procedures will help maintain a safe working environment. Compliance with industry standards and regulations is essential to protect workers and equipment.
Potential Challenges in Implementing Assembly Automation
Implementing assembly automation presents several challenges that need careful consideration. These challenges include:
- High initial cost: The significant upfront investment can be a barrier. This is especially true for small and medium-sized enterprises.
- Maintenance and repair: Automated systems may require regular maintenance and timely repairs. Manufacturers may require skilled technicians for these tasks.
- Integration with existing systems: Integrating new automation technology with existing manufacturing processes can be complex and time-consuming.
- Workforce training: Training employees to operate and maintain automated systems is crucial. This may involve a steep learning curve and additional training costs.
- Resistance to change: Employees may resist the transition to automation. Reasons could include the fear of job loss or unfamiliarity with new technologies.
Transform Your Manufacturing With the Bihler Group of Companies
Integrating automated assembly lines into your manufacturing processes can significantly enhance efficiency, product quality and scalability. However, navigating the complexities of automation requires a trusted partner with the expertise to tailor solutions to your specific needs.
Bihler of America excels in providing cutting-edge automated manufacturing solutions. With our extensive range of standard equipment and solutions you can tailor to your needs, Bihler helps you stay competitive in a rapidly evolving industry.
Contact us online to transform your manufacturing processes today.